Lycoming Service Instruction No. 1042
- Lycoming Service Instruction No. 1042 gives the specified plugs for all engine models. You will find Airworthiness Directives, Service Bulletins, Service Instructions and other informational publications through these links. You will also find other publications relating to.
- Latest revision Lycoming Service Instruction No. Clean engine. Inspect condition of spark plugs (clean and adjust gap as required, adjust per latest revision Lycoming Service Instruction no. NOTE: If fouling of spark plugs are apparent, rotate bottom plugs to upper plugs. Inspect spark plug cable leads.
Service Instruction No. Rotate top and bottom spark plugs every 25 to. Caution – Use only approved spark plugs for all models of Lycoming engines. See latest revision of Lycoming Service Instruction No. 1042 for approved spark. Apr 10, 2018. Service Instruction No. Service Instruction No.
Engine oil provides lubrication and cooling for an aircraft’s engine. Ensuring your oil pressure remains “in the green” is one of the most important things you can do for your engine’s health and longevity.Oil pressure in an engine is like blood pressure in a human. Both are important indicators of internal health, and both should be kept within proper parameters to ensure longevity. Operating pressureThe normal oil pressure range for most Lycoming engines is between 60 to 90 pounds per square inch (psi). This range is indicated by the green arc on the oil pressure gauge. The maximum oil pressure allowed for short durations is 115 psi on most models.
Lycoming Break In Instructions
The maximum allowable pressure has increased over the years from 100 to 115 psi. The top red line on most oil pressure gauges is 100 psi. The lowest allowable limit for oil pressure with the engine operating at idle with hot oil is 25 psi, which is indicated by the lower red line on most oil pressure gauges.Lycoming generally sets the operating pressures for cruise rpm on their factory-rebuilt engines to between 75 to 85 psi. Most new, rebuilt or overhauled engines require a slight adjustment of the oil pressure to finalize the setting once the engine break-in process is complete.Oil flow through a typical Lycoming engineLycoming engines use a “wet sump” oil system. This simply means that the oil sump is mounted under the engine and oil flows by means of gravity back to the sump after it has been pumped through the engine. The sump is completely open on the top so that all areas of the engine can drain back into it, and it functions like a large drain pan.
“Dry sump” systems have a separate dedicated oil tank. Oil is routed to the tank once it has completed its course through the engine.The Lycoming oil pump is located in the accessory housing. It consists of an aluminum outer body and two steel impellers, one of which is gear-driven off the crankshaft. (See photos 01 and 02, this page and photo 03, page 35.) It produces oil pressure in direct proportion to how fast the gears spin. At higher engine rpm, the pump produces more oil pressure than at low engine rpm.Oil is drawn up through the suction screen in the sump and through the oil pump impellers. The oil is then routed to the thermostatic bypass valve (also called a vernatherm valve).Oil continues to flow to the oil filter adapter on the accessory case and through the oil filter (or screen if the engine is not equipped with an oil filter).
From the filter, oil is routed to the oil pressure relief valve. The oil pressure relief valve is located on the top right side of the crankcase. It relieves excessive oil pressure by opening a drain port to the sump to bypass some of the oil flow if oil pressure gets too high.Oil then travels to the crankshaft bearings and through predrilled passageways in the case to lubricate the internal engine parts through either pressure or splash lubrication. After completing its course, the oil drains back to the sump.Thermostatic bypass valveThe thermostatic bypass valve is similar to a thermostat in an automotive engine cooling system.
(See photo 04, page 35.) The valve remains open when the oil is below 180 F, allowing the oil to bypass the passage to the oil cooler. As the oil heats up past 180 F, the vernatherm expands and eventually contacts its seat, forcing oil to pass through the oil cooler.An engine that has abnormally high oil temperature may have a thermostatic bypass valve that is not expanding as it should with increased temperature, or that is not seating properly due to a worn seat.

Lycoming Service Instruction No. 1042 For Approved Equipment
The valve seat wears over time and typically gets a worn groove that gets slightly worse every time it closes. If the valve gets excessively worn it allows some oil to bypass the oil cooler even when the oil is hot. (See photo 05, page 35.) Some of the older bypass valves had retaining nuts that were improperly crimped during manufacture.
Lycoming issued Mandatory Service Bulletin 518C that contained instructions for performing a heat treatment using a special Loctite to permanently secure the nuts in place. Valves that have had the Loctite treatment are typically inscribed with an “L” near the part number to indicate they have been repaired.As of August 2016, Lycoming no longer recommends this repair. Mandatory Service Bulletin 518D supersedes 518C and states that valve repair/rework is no longer allowed.
Older-style valves with loose crimp nuts should be replaced.Engines that suddenly develop an oil temperature problem may have one of the older-style valves with an improperly crimped nut that has come completely loose. Lycoming Service Instruction 1565 provides the procedure for replacement.Oil pressure relief valveThe oil pump is a direct drive pump. This means that the pump impellers spin in direct relation to engine speed and produce oil pressure that also varies directly with engine speed.At high engine rpm, the pump produces far more pressure than the engine is designed to handle. Therefore, a pressure regulator must be incorporated into the system to keep pressures high enough at low engine speeds to protect the bearings and low enough at high engine speeds to prevent rupturing or damaging any of the engine components.The oil pressure relief valve (or oil pressure regulator) is located on the top right side of the crankcase; behind the number three or the number five cylinder, depending on whether it’s a four- or six-cylinder engine. (See photo 06, page 36.)The oil pressure relief valve is very basic in its method of relieving excessive oil pressure.
It consists of an aluminum housing with a strong spring, which presses against a steel ball. The spring keeps the ball seated.As oil pressure builds beyond the amount the spring is adjusted to maintain, the ball is forced off its seat by the excessive pressure.
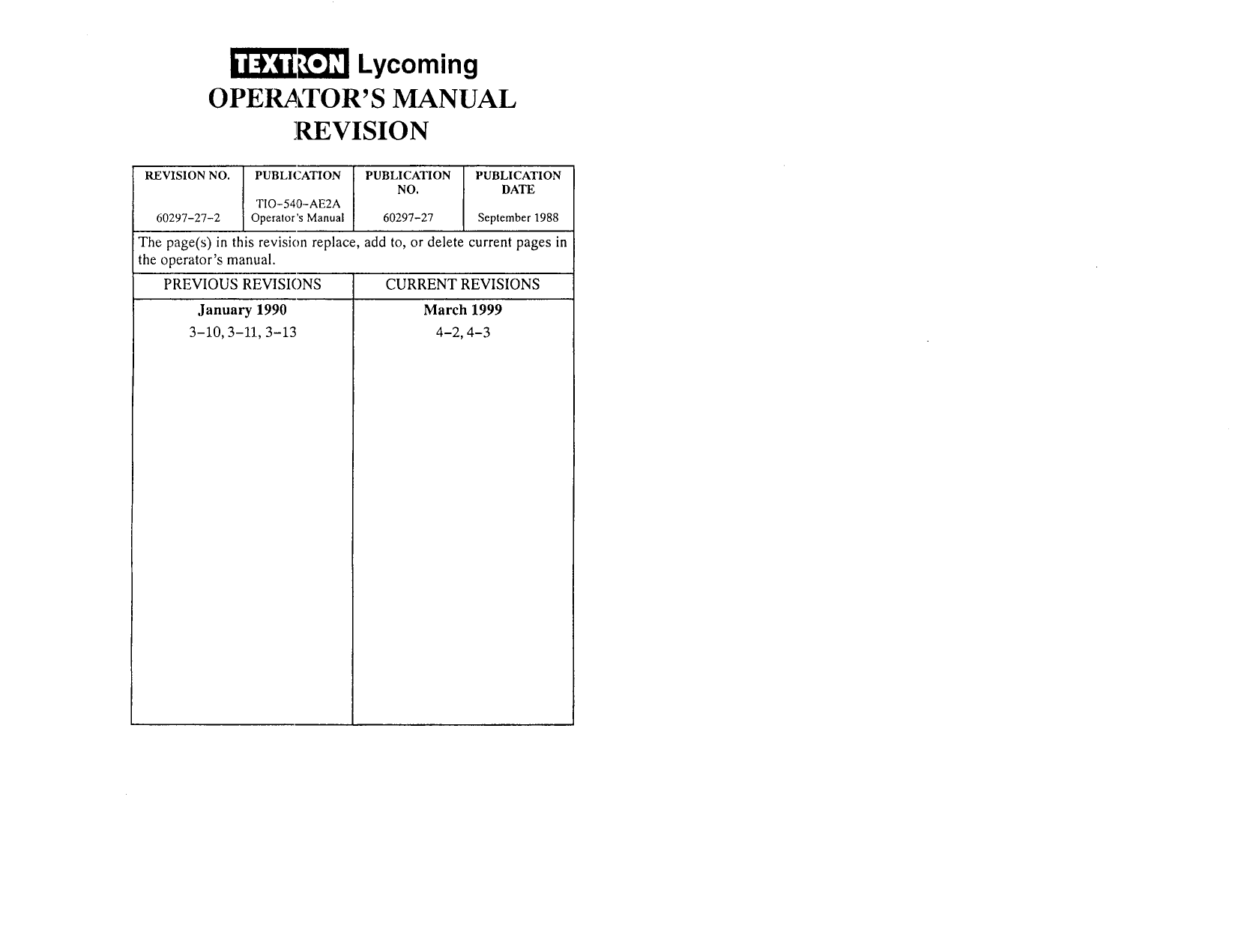
This exposes a passageway (bypass) that directs excess oil back to the sump, relieving some of the oil pressure.There are three types of housings. The latest style has an adjustable spring seat that can be cranked in or out as needed by means of an attached castellated nut on the end of the shaft.The older styles were adjusted by removing the housing and spring and adding or subtracting washers behind the spring to increase or decrease pressure.
(See photos 07 and 08 on page 36 and photo 09 on page 38.)The oldest style housing was short and had an adjustment of zero to three washers maximum. (See photo 10, page 38.) The longer housing allowed up to nine washers maximum to increase spring tension.
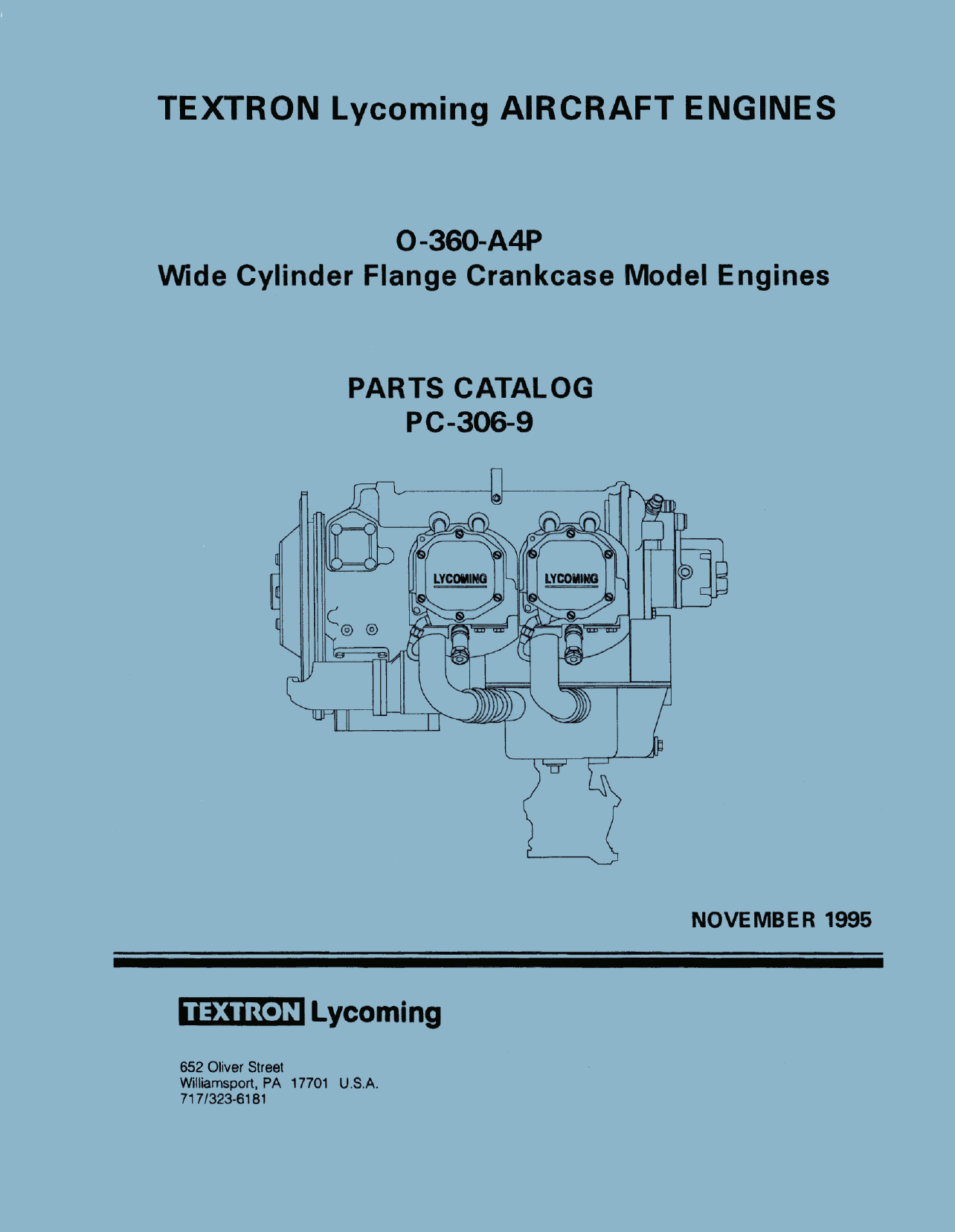
(See photo 11, page 38.) Each added washer increases oil pressure approximately 5 psi. On the externally adjustable models, one turn in (clockwise) increases oil pressure approximately 5 psi.There are also springs of varying tensions and lengths which can be interchanged if the above adjustments do not yield the desired results. Some of the springs are color-coded to help differentiate them from one another. The most commonly used ones are the white LW-11713 springs (thick, heavy springs that are used to increase oil pressure at all settings), the 68668 (purple springs that are short and have much less tension than the others), and the 61084 non-color-coded spring that is standard equipment on most regulators. (See photo 12, page 40.)One of the more common problems with the oil pressure regulators is with the seat that the steel ball contacts every time it closes. The seat is simply a machined aluminum section of the crankcase itself on most engine models, and over time it can become worn, especially if the ball is not contacting the seat dead in the center.If oil pressure varies excessively with engine rpm, especially at lower engine speeds, the regulator ball and seat may not be closing properly.
Poor contact allows some of the oil to bypass back to the sump when it shouldn’t.
Yes the game works on Windows 7 but you'll have to install and run the game as an administrator at all times. View in thread. Question is can I play CC&C the first decade in win 7, if all I have is win 7 on this PC how can it run in a older OS. Command and conquer the. Then I'd say, install the community patch I linked to in my first reply. It makes all the games no-cd. Do note that for C&C1, RA1 and TS there have.